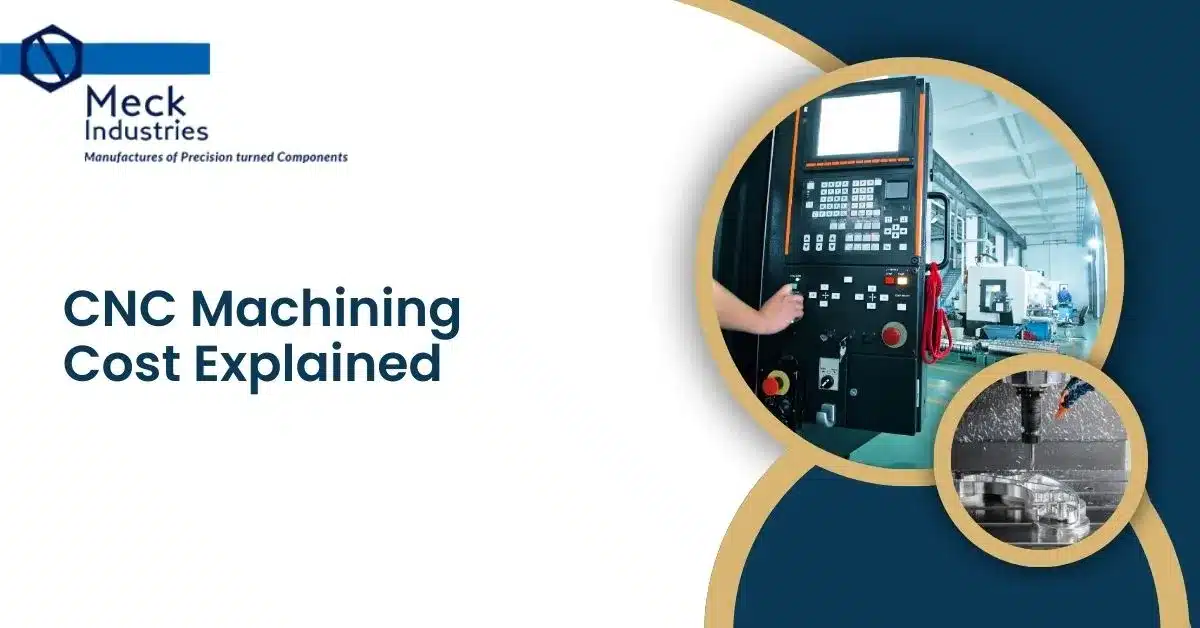
CNC (Computer Numerical Control) machining is a popular manufacturing process that uses computerized tools to create precise parts from various materials. Understanding the factors influencing CNC machining costs can help businesses optimize their budgets and production processes.
CNC Machine Parts
CNC machines consist of several essential components that contribute to their efficiency and precision. Key parts include:
- Control Panel – The interface where operators input commands and monitor the machining process.
- Spindle – Rotates cutting tools at high speeds for material removal.
- Tool Holders – Secure the cutting tools in place during operations.
- Linear Guides and Rails – Ensure precise movement of machine components along the X, Y, and Z axes.
- Worktable – The surface on which raw materials are clamped for machining.
- Coolant System – Regulates temperature and removes debris during cutting.
- Servo Motors and Drives – Provide accurate motion control for various machine axes.
- Chip Conveyor – Removes chips and waste material from the machining area.
Factors Affecting CNC Machining Costs
- Material Selection
- The choice of material significantly impacts the cost. Common materials include aluminium, steel, brass, and plastics, each varying in price and machinability.
- Complexity of Design
- Intricate designs require more time and expertise, increasing both labour and machine time costs.
- Production Volume
- Higher volumes reduce per-unit costs due to economies of scale, while small batch productions can be more expensive.
- Machine Time
- The longer the machine runs, the higher the cost. Advanced CNC machines may have higher rates but can complete jobs faster.
- Labor Costs
- Skilled machinists and operators are required to manage and maintain CNC machines, contributing to the overall expense.
- Post-Processing
- Additional processes like polishing, coating, or assembly add to the final cost.
- Tooling and Setup
- Custom tooling and fixture creation incur additional costs, especially for complex or specialized projects.
Looking for high-quality CNC machine parts? Get reliable components designed for precision and durability. Contact us today for expert guidance!
Tips to Reduce CNC Machining Costs
- Choose cost-effective materials that meet design requirements.
- Simplify designs to minimize machining complexity.
- Optimize production volumes to benefit from bulk pricing.
- Collaborate with experienced CNC machinists for efficient planning.
- Minimize post-processing needs where possible.
Frequently Asked Questions
Which materials are most cost-effective for CNC machining?
Aluminium and plastics are generally more affordable and easier to machine, making them cost-effective options.
Does design complexity impact CNC machining costs?
Yes, complex designs with intricate details require more machine time and labour, increasing the overall cost.
How can I reduce my CNC machining costs?
Simplify your design, select cost-effective materials, increase production volume, and minimize post-processing to lower costs.
Is CNC machining suitable for low-volume production?
While CNC machining is cost-effective for medium to high-volume production, it can also be used for low volume runs, especially for prototypes and specialized parts.
Conclusion
Understanding CNC machining cost factors can help businesses make informed decisions, balancing quality and budget. By optimizing design, material selection, and production strategies, companies can achieve cost-effective manufacturing solutions. For further insights and assistance, consult with CNC machining experts.