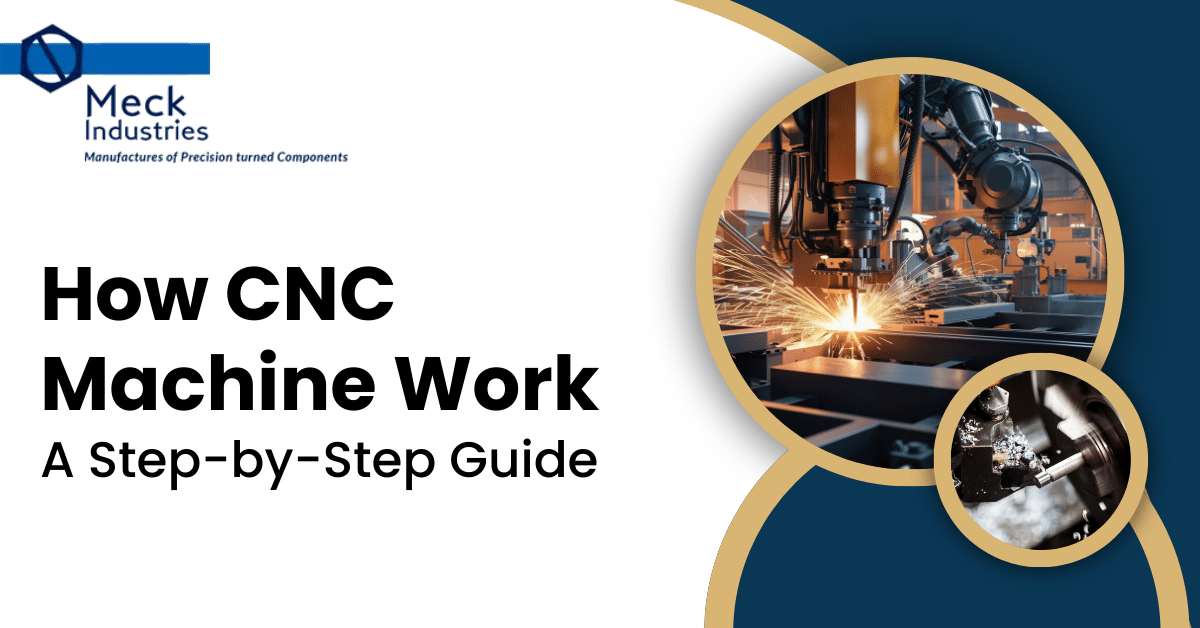
CNC Machines have revolutionized the manufacturing industry by providing Unmatched Precision, Automation, and Efficiency. Whether you’re producing Intricate Parts for Aerospace or Simple Components for everyday Machinery, CNC Machines ensure Consistency and Quality. In this Guide, we’ll take you through the complete process of CNC Machining, explaining each Step from Design to Final Product.
What is a CNC Machine?
A CNC Machine, whose full form is Computer Numerical Control Machine, is a highly automated device that interprets digital instructions to control tools and machinery, producing precision components. Unlike manual machining, CNC machines rely on pre-programmed computer software to guide their movements, reducing the need for human intervention. CNC machines come in various types—such as milling machines, lathes, and routers—each designed for different manufacturing tasks.
Step-By-Step Process of CNC Machining Working
Let’s walk through the step-by-step process of how CNC machining works.
Step 1: Designing the Part
The first step in any CNC machining process is designing the part using CAD (Computer-Aided Design) software. This is where the engineer or designer creates a digital model of the part that will be manufactured. CAD software allows for intricate detailing and precision, enabling the design of complex shapes that would be difficult or impossible to make manually.
Once the design is complete, it is saved in a digital format (usually a CAD file) and passed on to the next stage.
Step 2: Generating the CNC Program
Next, the CAD file is converted into a CNC program through CAM (Computer-Aided Manufacturing) Software. CAM software translates the 3D design into machine-readable instructions, primarily in the form of G-code and M-code. These codes define tool movements, cutting speeds, and specific machining processes.
The CNC program serves as the roadmap that tells the machine exactly how to shape, cut, and finish the material, ensuring precision throughout the operation.
Step 3: Setting Up the CNC Machine
Once the CNC program is ready, it’s time to set up the machine. This involves loading the material onto the machine bed, installing the appropriate tools (such as drills, mills, or lathes), and configuring machine parameters like tool speeds, feed rates, and tool alignment. Depending on the complexity of the job, this setup phase may also include calibrating sensors and ensuring that all safety measures are in place.
Step 4: Machining Operations
Now, the actual machining begins. The CNC machine follows the programmed instructions to cut, drill, or shape the material. Depending on the type of machine and material, different machining operations are performed. For instance:
- Milling: Rotating tools cut away material to create the desired shape.
- Turning: Material is rotated while a stationary tool shapes it, typically used for cylindrical parts.
- Laser Cutting: A high-powered laser precisely cuts or engraves the material.
The machine may change tools automatically as per the program, ensuring different cuts and operations are performed without human intervention.
Step 5: Monitoring the CNC Machining Process
Although CNC machines operate autonomously, monitoring is crucial. Operators keep an eye on the machine’s performance to ensure everything runs smoothly. In real-time, they can check for deviations or errors and make adjustments if necessary. The CNC machine’s high level of automation reduces the chances of mistakes, but human oversight ensures that any issues are quickly addressed.
Step 6: Finishing and Post-Processing
Once the machining process is complete, the part often requires finishing. This might involve cleaning, polishing, or deburring to remove sharp edges and improve the surface finish. In some cases, parts may need additional post-processing steps such as heat treatment or coating to enhance their durability or appearance.
After finishing, the final product undergoes a thorough inspection to ensure it meets the specified design and quality standards.
Common CNC Machining Materials
CNC machines can work with a wide variety of materials, depending on the requirements of the part. Some common materials used include:
- Metals: Aluminum, brass, copper, stainless steel, and titanium are popular choices due to their strength and versatility.
- Plastics: ABS, polycarbonate, and nylon are often used for lighter, less expensive parts.
- Wood: CNC routers are often used to carve wood for furniture, signage, and other decorative items.
Each material has its machining properties, which affect tool selection, cutting speeds, and other parameters.
Advantages of CNC Machining
CNC Machining offers numerous benefits over traditional manual methods. Some of the key advantages include:
- Precision: CNC machines provide extremely high accuracy, making them ideal for applications where tolerances are critical.
- Efficiency: Once programmed, CNC machines can operate continuously, drastically reducing production time.
- Consistency: CNC machining ensures uniformity across large production runs, eliminating variations between parts.
- Flexibility: With the right program, a CNC machine can create complex designs and switch between different jobs quickly.
How Meck Industries can help with Custom CNC Machining
At Meck Industries, we specialize in delivering high-quality Custom CNC Machining Solutions tailored to your specific needs. Our expertise in precision manufacturing ensures that every component we produce meets the highest standards of accuracy and durability. Whether you’re in need of complex parts for aerospace, automotive, or industrial applications, our advanced CNC machining technology allows us to work with a wide range of materials, including metals like Aluminum, Brass, Copper, and More.
We offer end-to-end support from initial design to final production, providing solutions that improve efficiency, reduce costs, and ensure the timely delivery of your custom parts. With a commitment to quality and customer satisfaction, Meck Industries is your trusted partner for Custom CNC Machining.
Frequently Asked Questions
What is CNC Machining used for?
CNC machining is used to manufacture parts and components for various industries, including automotive, aerospace, electronics, and woodworking. It is particularly beneficial for producing intricate designs and prototypes with precision.
How does CNC machining work?
CNC machining works by converting a digital design into machine-readable instructions that guide the machine to cut, shape, or engrave materials with extreme precision.
What Materials Can CNC Machines Process?
CNC machines can process a wide range of materials, including metals (like aluminum and brass), plastics, wood, and even glass.
What is the Difference Between CNC Machining and 3D Printing?
CNC machining is a subtractive process where material is removed to form the final shape, while 3D printing is an additive process where layers of material are built up to create a part.
How Accurate is CNC Machining?
CNC Machines can achieve tolerances as tight as 0.001 inches, depending on the material and the complexity of the design.
Conclusion
CNC machining has become a cornerstone of modern manufacturing, offering incredible precision, automation, and versatility. From the initial design to the final product, understanding how CNC machines work is key to unlocking their full potential. Whether you’re working with metals, plastics, or wood, CNC machining ensures that your parts are crafted to perfection.
If you’re looking for reliable CNC machining services, choose a manufacturer with expertise and experience to ensure your components meet the highest quality standards.